In today’s fast-paced and competitive business environment, organizations are constantly looking for ways to improve efficiency, reduce waste, and streamline their processes. A proven strategy for achieving these objectives is to adopt the principles of lean manufacturing and establish a lean culture.
Businesses can cultivate a culture that fosters innovation, increases productivity, and provides exceptional customer value by encouraging teamwork, a mindset of continuous improvement, and the reduction of waste. In this article, we’ll look at how to effectively apply the key principles of lean manufacturing to create a lean culture in your company.
Key Principles of Lean Manufacturing and Its Application
-
Principle of Value
Understanding and delineating what customers really value is the first step in creating a lean culture. Businesses can align their processes and activities to produce value-driven outcomes by concentrating on the requirements and expectations of customers. By eliminating non-value-adding activities and optimizing processes that create value, this principle encourages businesses to streamline their operations and ensures that every step in the value chain directly contributes to customer satisfaction.
-
Principle of Continuous Improvement
Continuous improvement lies at the heart of lean manufacturing and building a lean culture. It involves giving employees at all levels the authority to find and get rid of waste, reduce variation, and look for ways to improve. Organizations can achieve incremental improvements and maintain a competitive edge by encouraging a culture of continuous learning, experimentation, and problem-solving. Engaging employees, encouraging their suggestions and ideas, and providing them with the tools and resources they need to contribute to ongoing improvement efforts are all emphasized in this principle.
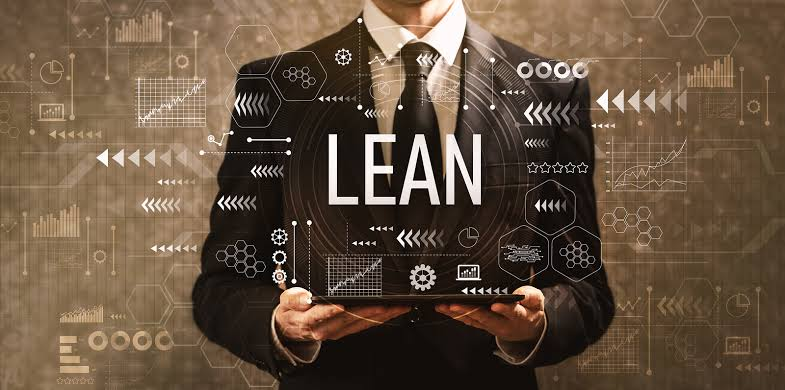
Building a Lean Culture: Embracing the Principles of Lean Manufacturing
-
Principle of Flow
The goal of the principle of flow is to ensure that workflows run smoothly and without interruption. By optimizing the flow of materials, information, and activities, organizations in a lean culture strive to eliminate bottlenecks, delays, and excess inventory. Businesses can reduce lead times, increase overall productivity, identify and address process inefficiencies by mapping and analyzing value streams. To guarantee that work proceeds in a consistent and smooth manner, this principle encourages cross-functional collaboration, visual management, and the implementation of pull-based systems.
-
Principle of Pull
The pull principle emphasizes the significance of producing in response to customer demand and is closely related to the flow principle. By implementing pull-based systems that enable production to be initiated only when there is a customer need, businesses in a lean culture strive to avoid overproduction. Organizations can reduce inventory, reduce waste, and improve customer responsiveness by aligning production levels with actual demand. Additionally, this principle encourages a proactive approach to supply chain management, in which actual consumption rather than forecasts are used to replenish resources and materials.
-
Principle of Respect for People
The importance of valuing and empowering employees is recognized by the principle of respect for people. Fostering an atmosphere of trust, mutual respect, and collaboration is essential to the development of a lean culture. Employees are encouraged to participate in decision-making processes, receive the necessary training and development opportunities, and a culture of open communication and continuous learning is established by businesses that adhere to this principle. Businesses can increase employee engagement, unleash the full potential of their workforce, and cultivate a sense of ownership and pride in their work by investing in their people.
Conclusion
Adopting the principles of lean manufacturing is necessary for the development of a lean culture. Organizations can cultivate a culture of efficiency, innovation, and continuous growth, laying the groundwork for long-term success by focusing on customer value, flow, pull systems, and respect for people.